Manufacturing downtime is a major financial and operational burden for businesses. While equipment failures and supply chain disruptions contribute to lost productivity, one of the most underestimated causes of downtime is human error. Whether due to misconfigurations, lack of proper training, or procedural mistakes, human errors can significantly impact production efficiency and lead to substantial financial losses. In this article, we will explore the true cost of downtime caused by human error, its long-term impact on business performance, and how implementing effective work instructions can mitigate these risks.
The Financial Cost of Downtime in Manufacturing
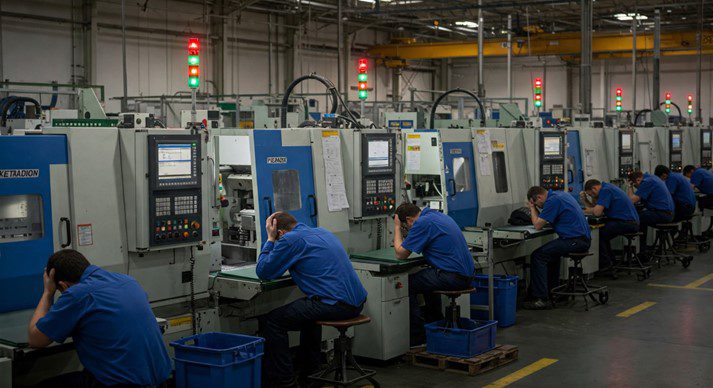
Downtime, defined as any period during which a manufacturing facility ceases production due to unexpected failures or delays, costs global manufacturers trillions of dollars annually. According to the Siemens 2024 Report on the True Cost of Downtime, the world’s 500 largest companies lose approximately $1.4 trillion per year due to unplanned downtime—11% of their annual revenues.
Cost Per Hour of Downtime by Industry
The financial losses incurred due to downtime vary significantly across industries:
- Automotive Industry: An hour of downtime costs $2.3 million—or $600 per second.
- Heavy Industry: Downtime costs have risen 4x since 2019, reaching $59 million annually per plant.
- Fast-Moving Consumer Goods (FMCG): The cost per hour is $36,000.
- Oil & Gas: Costs have fluctuated depending on global oil prices, reaching record highs in 2022.
The increase in downtime costs has outpaced inflation, particularly in Automotive (113%) and Heavy Industry (319%) since 2019.
How Much Does Human Error Contribute?
While downtime has multiple causes, studies indicate that human error is responsible for nearly 23% of unplanned downtime incidents in manufacturing. Human-related downtime results from:
- Operator Mistakes – Misconfiguring machines, skipping quality checks, or failing to follow safety procedures.
- Poor Maintenance Practices – Inadequate troubleshooting, failure to identify warning signs, or incorrect repair techniques.
- Lack of Training – Workers unfamiliar with machinery or software can make costly errors.
- Inadequate Documentation – Poorly written work instructions lead to inconsistent or incorrect execution of tasks.
For a large-scale automotive facility, this means that human error alone could be responsible for over $500 million in annual losses.
While the direct costs of downtime are significant, the long-term business implications can be even more damaging. Companies that fail to address human error in their production lines risk:
Long-Term Business Impact of Human-Related Downtime
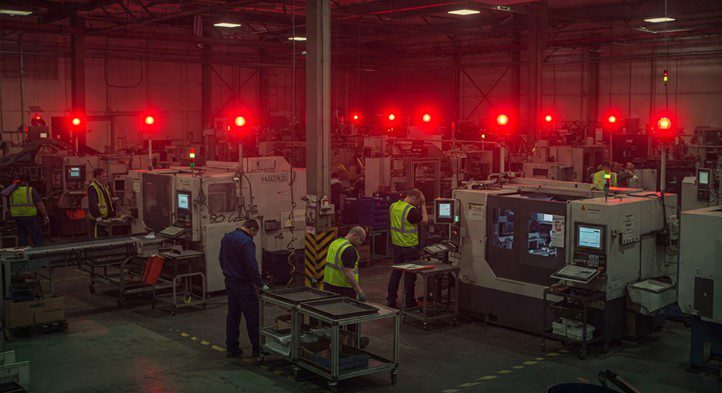
1. Damage to Reputation and Customer Trust
In manufacturing, meeting delivery deadlines is critical. Frequent production stoppages due to human error can cause missed shipments, delayed product launches, and contract penalties. In industries like automotive and aerospace, delays in delivering key components can disrupt entire supply chains.
For example:
- A major automotive company lost $750 million in a year due to frequent downtime issues.
- Small and Medium Enterprises (SMEs) risk losing major contracts if they fail to meet On-Time, In-Full (OTIF) delivery commitments.
2. Higher Operational Costs
Downtime not only results in lost production but also increases labor costs. When human error leads to a production halt, companies must often pay overtime wages to make up for lost output. Other cost implications include:
- Emergency repairs and maintenance – Last-minute fixes cost significantly more than scheduled maintenance.
- Wasted raw materials – When production stops midway, materials may need to be discarded.
- Penalties for contract violations – Suppliers can face hefty fines for delays.
3. Increased Employee Turnover and Low Morale
Human error-related downtime can create a high-pressure environment for workers. Employees may feel stressed, overworked, or under-trained, leading to higher turnover rates. A high turnover rate increases hiring and training costs, further exacerbating downtime issues.
4. Supply Chain Disruptions
Modern manufacturing relies on just-in-time (JIT) inventory systems to minimize costs. However, when human error causes unexpected downtime, companies must:
- Rush-order materials at premium costs.
- Miss scheduled deliveries, leading to financial penalties.
- Experience a ripple effect in the supply chain, causing delays for customers.
The Role of Good Work Instructions in Preventing Downtime
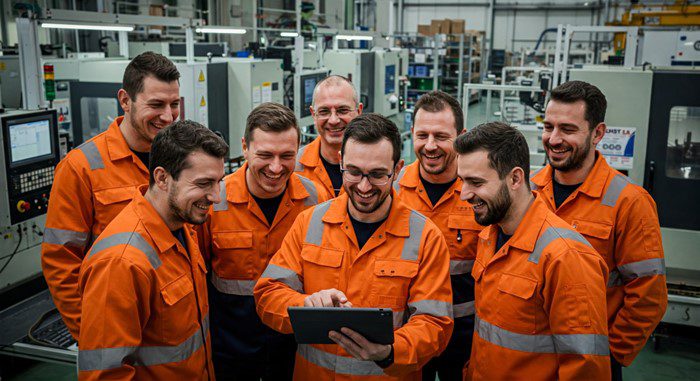
One of the most effective ways to reduce human error and prevent downtime is through well-structured, easy-to-follow work instructions. Companies that invest in digitized, standardized procedures see significant reductions in downtime-related losses.
Key Benefits of Effective Work Instructions
- Standardized Workflows: Clearly defined steps reduce variability and inconsistency, ensuring every employee follows best practices.
- Improved Training Efficiency: Work instructions serve as training guides for new employees, reducing the risk of costly mistakes.
- Faster Troubleshooting: When errors do occur, employees can quickly reference instructions to resolve issues, minimizing downtime.
- Reduced Cognitive Load: Step-by-step instructions make it easier for operators to focus on execution rather than recalling complex procedures.
- Real-Time Updates: Digital work instructions can be updated instantly when processes change, preventing outdated practices.
How Work Instructions Reduce Human Error
A study by the National Institute of Standards and Technology (NIST) found that structured work instructions reduce manufacturing errors by up to 40%.
Additionally, companies that digitized their work instructions saw a 35% improvement in adherence to safety protocols and a 50% reduction in misconfigurations.
Conclusion
Human error remains a major contributor to manufacturing downtime, leading to billions in lost revenue annually. While many companies focus on predictive maintenance (PdM) and automation, the simplest and most effective way to mitigate human-related downtime is to implement clear, standardized, and accessible work instructions.
By investing in structured documentation, digital work guides, and continuous employee training, manufacturers can reduce errors, increase efficiency, and protect their bottom line.
Key Takeaways
✅ Downtime costs the world’s largest companies $1.4 trillion annually, with human error responsible for nearly 23% of incidents.
✅ The automotive sector loses $2.3 million per hour of downtime, with costs increasing 113% since 2019.
✅ Poor training, inconsistent workflows, and lack of clear work instructions are major contributors to human-related downtime.
✅ Companies that implement digitized, real-time work instructions see up to a 47% reduction in human error-related downtime.
By addressing human error with structured processes and training, manufacturers can minimize downtime and drive long-term business success.