As businesses look to reopen and get employees back to work, there’s a highly effective technique that can help speed up the process — it’s called a Gemba Walk. The Gemba walk is an essential part of the Lean manufacturing philosophy. Its initial purpose is to allow managers and leaders to observe the actual work process, engage with employees, gain knowledge about the work process, and explore opportunities for continuous improvement.
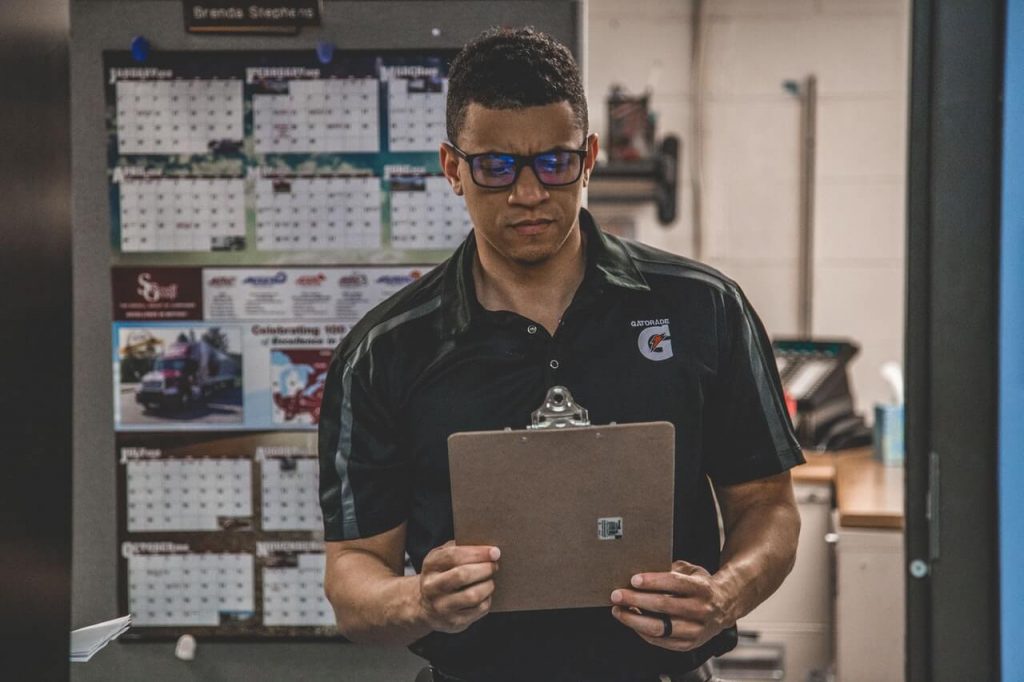
What is a Gemba Walk?
The translation of the term from the root Japanese word is “the real place.” It also is known as “the place where value is created.” In the practice of Lean and Six Sigma, it means taking the time to watch how a process is done and talking with those who do the job. So a Gemba Walk it a Japanese term that’s part of lean and Six Sigma practices. It means walking through your business and shop floor, taking the time to see how your company operates, how processes are done, and talking in detail with the people and team members who are doing your work. The Gemba walk is a concept developed by Taiichi Ohno, who is often considered the father of Just-in-time production.
There are 3 important elements of this lean manufacturing tool:
- Go and see. The main idea of the Gemba walk is for managers and leaders on every level to take regular walks around the shop floor and to be involved in finding wasteful activities.
- Ask why. A Gemba walk’s main objective is to explore the value stream in detail and locate its problematic parts through active communication. A good leader is always eager to listen rather than talk. Here is why you may use different techniques such as 5 whys in order to identify problematic parts of the process.
- Respect people. Keep in mind that a Gemba walk is not a “boss walk”. Pointing fingers and blaming people is exactly what you don’t have to do. You are not there to judge and review results. You are there to collaborate with the team and find problems together. Try to focus on finding the weak spots of the process, not of the people.
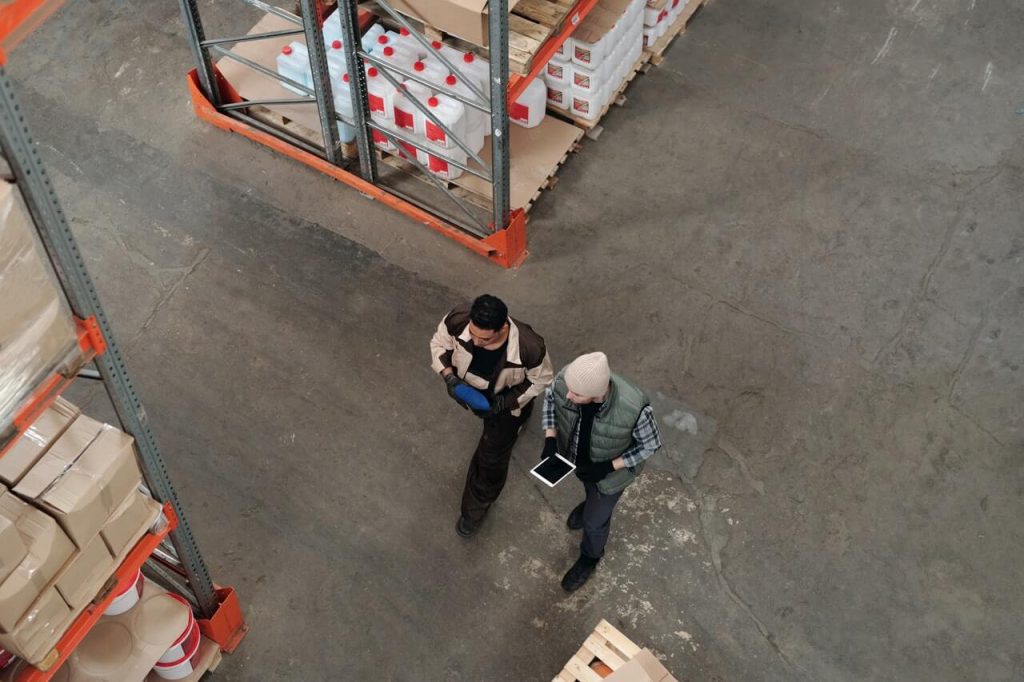
How to improve your Gemba walks?
Step 1: Identify the Purpose for the Gemba Walk
Before you go on any Gemba Walk, you must identify what is the purpose of the Gemba Walk and what is the theme. You might be looking for ways to improve productivity, reduce costs, reduce errors, improve flow or help facilitate improvement ideas. But you need to be clear on the purpose otherwise you will get lost and tied up in whatever is happening on the floor without clear improvements and outcomes.
Step 2: Ensure you understand the process you are about to observe in your Gemba Walk
If you do not know the high-level process that you are about to observe, the chances are that you will not be able to fully grasp the opportunities that exist. So before you begin any Gemba Walk, make sure you understand what you are about to observe so that you can provide the necessary support, guidance and insights.
Step 3: Select a time you will be observing
The Gemba Walk is about mutual respect and a joint interest in making processes faster, safer, easier and just plain better, so it’s not about catching people out. Setting a time makes sure that the team can be made aware and that team leaders can be available to engage in their part of the Gemba Walk.
Step 4: Select a time you will be observing
The Gemba means the place where “value is created” so do not get team members up to the office to debrief you. You must go to where the work is being done and where the value is created. In the famous lean phrase by Ohno, “every leader must wash their hands at least 3 times a day”.
Step 5: Spend time to Observe the Processes and quality of service provided
During the Gemba Walk, the goal is always to be focused on the process and what stops the process from achieving its goals of maximising customer value. So as you observe the process, consider the inputs into the process and are they fit for purpose. And how does the process, the inputs and the teams interact.
Step 6: Recognise how the process performs in its current state
Before jumping to solutions or opportunities, make sure you spend time observing and carefully understand how the current start is performing. Is the process performing as expected or is there delays, rework, confusion, movement etc?
Step 7: Visualise the gap between the ideal state and what actually happens
Now that you have understood the current status, what is the best ideal state and where are the gaps. The ideal state does not have to be a perfect future state but an achievable ideal state (given a number of restrictions). What you want to identify here is what is the gap that can potentially then be closed.
Step 8: Look for opportunities for improvements to close the gap
With a clear gap between the current and the ideal, what activities could be done by the team, managers, team leaders to help close this gap. Engage with the team, discuss options and build a document action plan for driving improvements.