Industrial manufacturers are one of the top adopters of Augmented Reality and immersive media in general. From asset design to instruction manuals, asset-intensive industries are implementing augmented reality experiences to provide immersive experiences for employees and customers.
Going from Text-based Instructions to Manuals 4.0
A user guide or user’s guide, also commonly known as a manual, is a technical communication document intended to give assistance to people using a particular system. It is usually written by a technical writer, although user guides are written by programmers, product or project managers, or other technical staff, particularly in smaller companies. Most user guides contain both a written guide and the associated images. In the case of computer applications, it is usual to include pictures or screenshots of the human-machine interface, and hardware manuals often include clear, simplified diagrams.
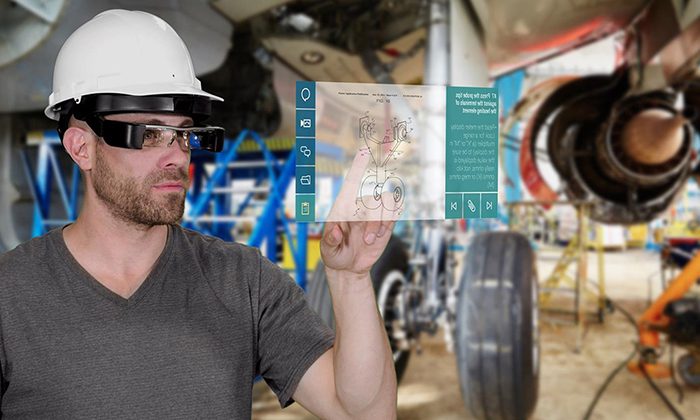
As Industry 4.0 and digital transformation get implemented across companies, this will change for sure. Manuals 4.0 will move away from text and images to become immersive visual guides that can guide unskilled people on how to resolve specific issues. Manuals 4.0 will also help get cross the current skill & knowledge gap that is plaguing the manufacturing world today. Going from paper-based written instructions towards digital visual gues will create an opportunity for equipment manufacturers and their buyers to transfer knowledge faster.
Managing Asset Inspection and Asset Maintenance
One of the key challenges with asset inspection has been that a user of an asset is not necessarily an expert on the asset. For example, a cook may not know what’s wrong with his oven or a production manager may not know the exact reasons for malfunctioning equipment. Traditionally, the way to get around this challenge was that experts would physically need to inspect the asset to check its condition.
Depending on the inspection, the expert would then need to take corrective action which often involved ordering new components and creating a maintenance schedule – this typically required two or three physical trips to the asset location. With remote assistance and visual guides, the requirement for a physical inspection can be reduced or even eliminated. Using augmented applications, asset conditions can be fully understood so that the expert can take corrective maintenance actions. Quite often this can be achieved virtually too. In either case, by using augmented reality, the experts do not require multiple trips to inspect, repair and maintain assets.
A well-known example is ThyssenKrupp Elevators. They use augmented and virtual reality to inspect elevators and repair them. One of the key advantages of their setup is that the technician is hands-free to carry out the repair and at the same time can uncover information about the elevator being repaired. Traditionally, this required accessing a laptop which meant the technician could either look at the information or carry out the repair. Their AR setup allows their technicians to do both. They suggest that a job which typically used to take one-to-two hours can now be carried out in less than twenty minutes.
AR Adoption Challenges
There are two main adoption challenges that AR applications are facing today:
- Miniaturization Issue – People prefer augmented reality headsets to be of the same size as normal eyeglasses. This is an adoption challenge as the functionality offered by AR headsets requires them to be bigger than normal eyeglasses.
- Digital Fatigue – Human beings are not used to augmented reality — the combination of spatial computing, as well as real-world information blended with virtual information, can cause digital fatigue.
Whilst there are always adoption challenges with any new technology, augmented reality is already influencing the asset lifecycle management of asset-intensive industries so much that they are one of the top four adopters of augmented technology.
The Common Sense Approach
As mentioned, there are existing challenges which preventing companies to leverage AR at its full potential. Not every company is ready to invest heavily in this new technology. There is also a learning curve that needs to be addressed. With this in mind, we decided to develop a more common sense product, that is device-agnostic and can easily be adopted in the manufacturing workspace. Later on, as AR headsets and smart glasses become more common, users can start to leverage more advanced features that come with higher immersion.
The product that we developed is called REWO. REWO is a video-based augmented reality platform which helps manufacturing companies record internal know-how & best practices and turn them into clear visual instructions for skilled trade workers so they can be better at their job. REWO gives your operators more ownership of their machines. Click here to try it out.