Customer-specific products are booming, wich means that batch sizes are getting smaller and smaller. As a result, the variation and combination of different tasks to be performed at a workplace and by an employee are also increasing sharply. An employee has to master an almost infinite number of processes. In order not to be overtaxed and not to forget anything during the process execution, he must be able to access the work instructions simply and quickly. At the same time, due to the shortage of skilled workers, companies face the challenge of training unskilled workers very quickly. All in all, good work instructions are an important tool of today’s lean manufacturers.
Procedures and protocols are a crucial focal point for both management and workers; to understand what the organisations minimum management expectations are and to provide instruction and guidance for work tasks for day-to-day operations, non-standard tasks and for emergency situations. The goal of standardization is to do more with less resources, less time, and less effort. You’ve probably already identified your best practices—the ones that preserve value while eliminating waste.
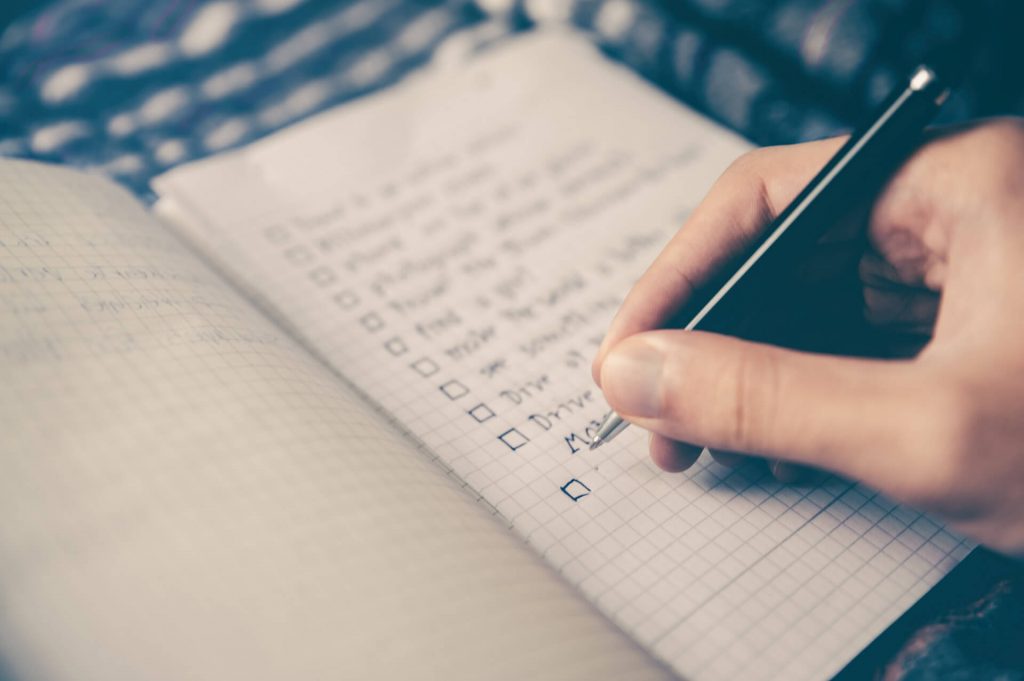
Why are work instructions they important?
Work instructions are created to guide workers in four key quality areas: training, reference, problem solving and continuous improvement. Use these four reasons to write useful work instructions.
Training new workers
Training is the essential first step to ensuring that people are competent in their duties. It is important to define, within the quality planning activities, the type of training that each function is to receive. It is equally necessary to ensure that the trainers are executing the plan, including improvements made to the instructions.
New employees should start their training with the process expert so they can observe how the process should be performed. It is here that detailed training discussions and hands-on activities take place between the expert and the trainee. The trainer uses the work instructions so new employees understand the basis for the tasks they are performing. The process is an opportunity for additional review of the work instruction content. The veteran can reaffirm the defined steps, and the new employee can confirm the validity of the process.
A measure of reference
This quality activity should focus on both access and format of the instructions. The documentation must be implemented so workers are not wary of having to locate the information relative to their areas of responsibility.
Once employees have been trained and have demonstrated that they can be effective performers, you must ensure that the work instructions are available in case of questions. The instructions must be presented in an easy-to-understand format so that access and review will not take up valuable time.
Write out how the instruction is to be performed specific to each core task. Avoid defining why the activity is performed. There should be no need for an expert organization to reaffirm why core tasks are needed. If the “why” information must be defined, keep that separate from the work instructions and make the additional information available as reference-only training documents.
Problem solving
Problem solving is a quality activity that focuses on ensuring that the supporting processes are properly defined to achieve product quality. Documentation should be referenced frequently to ensure that relevance is maintained.
Work instructions are key documents to reference when internal or external nonconformances are identified. Make the review of the work instructions part of the corrective action process. Ask if the supporting instruction properly defines the process, then audit the instruction to confirm proper definition.
The operator/employee cannot be held fully accountable if the records of training are written to an inadequately defined work instruction. If the task is properly defined, the manner by which training is conducted might need to be revisited.
Continuous Improvement
Work instructions should not be stagnant documents accessed only when auditors ask for them. Reviewing work instructions when improvement opportunities are identified demonstrates that they are “living documents.”
Instructions can be improved upon through document reviews, audits, a disciplined problem-solving process and, most importantly, the input from the experts who are performing the tasks. The current documentation should be the starting point for all improvements. Always improve upon existing documentation before creating a new document. Volume does not equate to continuous improvement.
Identifying that your work instructions serve four key purposes provides the evidence that your organization practices advanced quality planning. It shows that the organization considers the work instruction process to be more important than just a mandated requirement from the latest quality standard. It also demonstrates that top management understands the importance of ensuring that such documentation is properly created, implemented, used and improved upon.
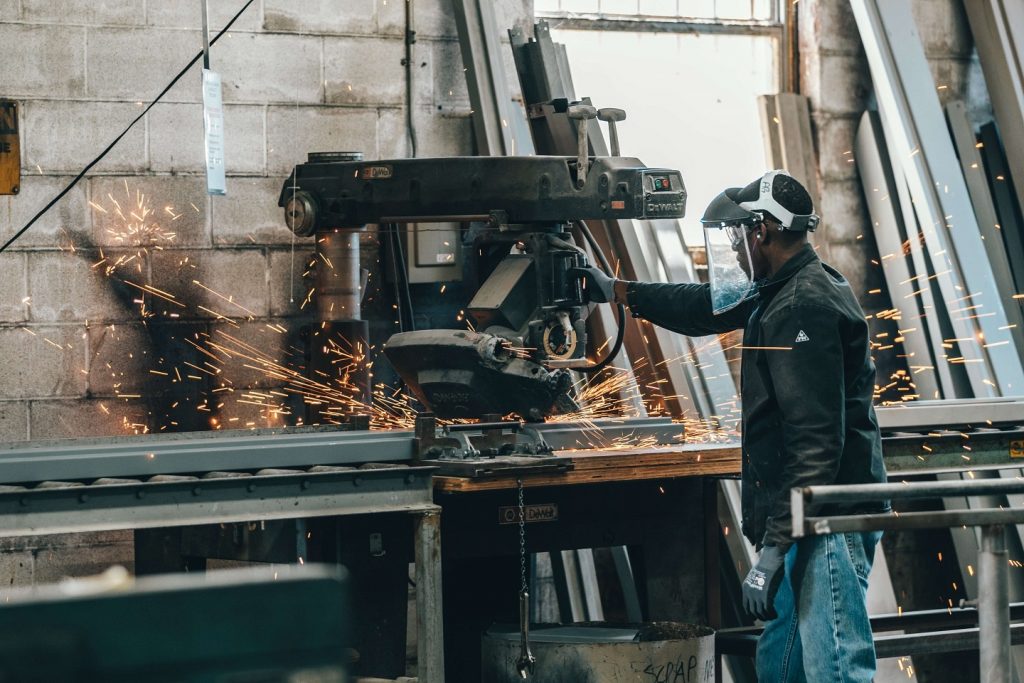
Without proper work instructions you will not be able to compete
The importance of high-quality work instructions is constantly increasing. In times of a shortage of skilled workers, small batch sizes and varied productions, precise work instructions are the gold of the 21st century. Find out here how to create a professional work instruction and what you have to pay attention to.