The new trading environment created by COVID-19 has left many manufacturers with a number of arising risks. The impact of the COVID-19 outbreak on supply chains will affect the manufacturing industry in several ways. Some of the effects might not have been anticipated and could leave businesses at more risk than anticipated. Companies using REWO were able to decrease some of these risks.
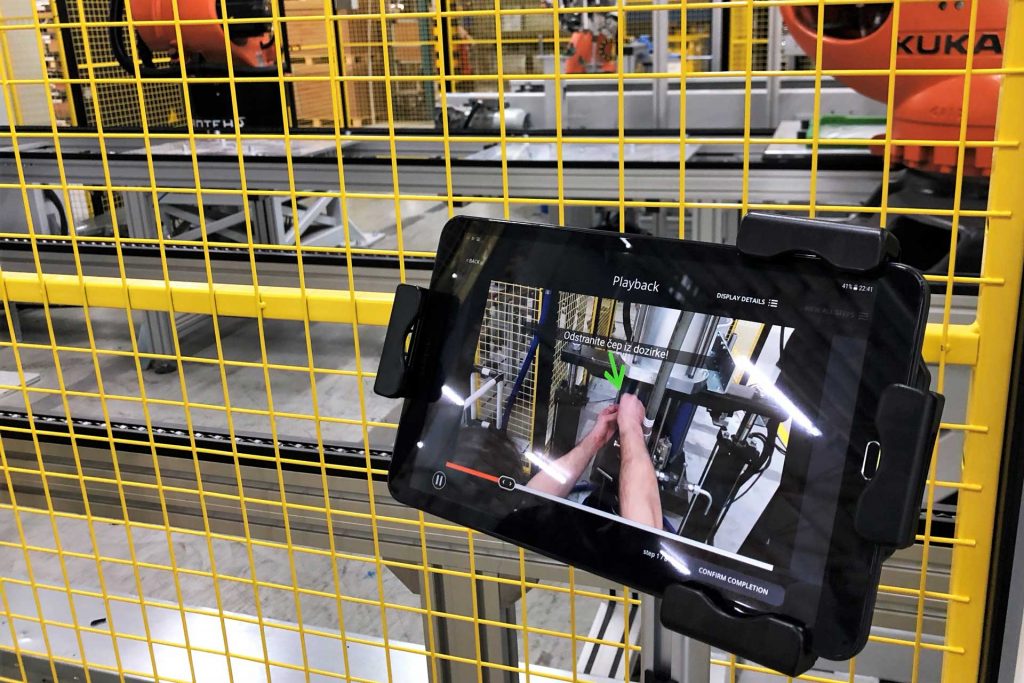
Reducing the risks when key knowledge holders got quarantined
During COVID many companies realized that it’s no longer feasible to rely on job-shadowing as the primary training method. Job-shadowing requires the availability of your most knowledgeable workers, who often have priorities other than training. And with COVID lurking you never know which of your employees might be quarantined.
Companies that are using REWO were able to quickly digitize key processes through visual work instructions. Key knowledge holders were able to record what they know and thus help their company be a bit more secure in case they would not be available to work or train new hires.
Contactless onboarding for new hires
Investing in innovative tools to improve employee onboarding and training can make all the difference during these pandemic times. Manufacturers using REWO were able to provide visual digital instructions to new hires and thus onboard them to their new positions without the need for extensive human contact. Modern technologies like these are key for faster and safer onboarding. New recruits felt excited to learn and confident in their ability to perform and improve procedures and the company was able to reduce risks by reducing in-person contact within the company.
Improved digital culture across the shopfloor
With any system for continuous improvement, the culture of your workforce has to be aligned with the goals. Talking about digitalization is not the same as seeing it and seeing its benefits. While the back office was already in the process of digitalization before COVID, the adoption of digital tools on the shop floor was lagging. Customers who used REWO were able to introduce a tool to their operators that clearly pointed out all the benefits of digital work instructions. Operators were able to clearly see the benefits and thus had a greater acceptance for other digital tools implemented later on.
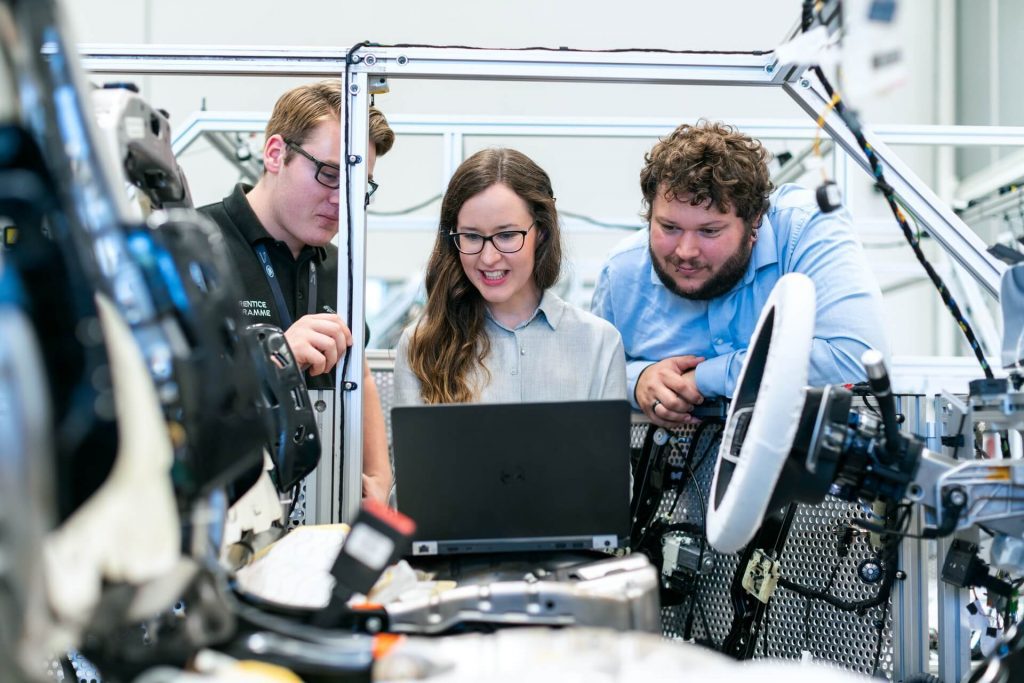
Final thoughts
While it’s true that manufacturing is faced with growing retirements, constant internal job changes, and training a new generation of workers, the core tenets of learning and workforce development remain the same. People need essential information to be presented clearly, with visuals, and on a regular basis. The best strategy for adapting to the shifting workforce is to find a digital tool that communicates clearly and regularly reinforces knowledge.