Digitization is radically changing the face of manufacturing companies. Digital factories are transforming manufacturing, as companies implement innovative technology and look for employees with fundamentally different types of qualifications. These new digital factories are being created in the heart of Europe to produce highly customized products and systems. One area that is receiving a lot of focus is training. Digital training is on its way to becoming the standard by scraping typical face-to-face mentoring sessions and replacing it with digital mentors that are always available to the company’s employees.
An extra boost to digital training
As manufacturers adjust their operational procedures to reduce physical contact among workers and ensure a two-metre distance between them, training has emerged as yet another obstacle to keeping production running.
As workers call in sick or are asked to self-quarantine, new-hires and existing workers need to be trained more quickly than ever to fill critical positions left open. And despite all the turmoil caused by COVID-19, yearly compliance training still has to be completed on time by all workers to prevent taking an audit hit and stay in business.
To achieve these training goals while keeping workers safe, manufactures have no choice but to replace their traditional classroom-style training and on-the-job shadowing with a digital alternative.
The benefits of enabling workers to learn autonomously at their workstations goes beyond just ensuring their safety. Workers also learn more quickly and effectively compared to traditional classroom training and on the job shadowing.
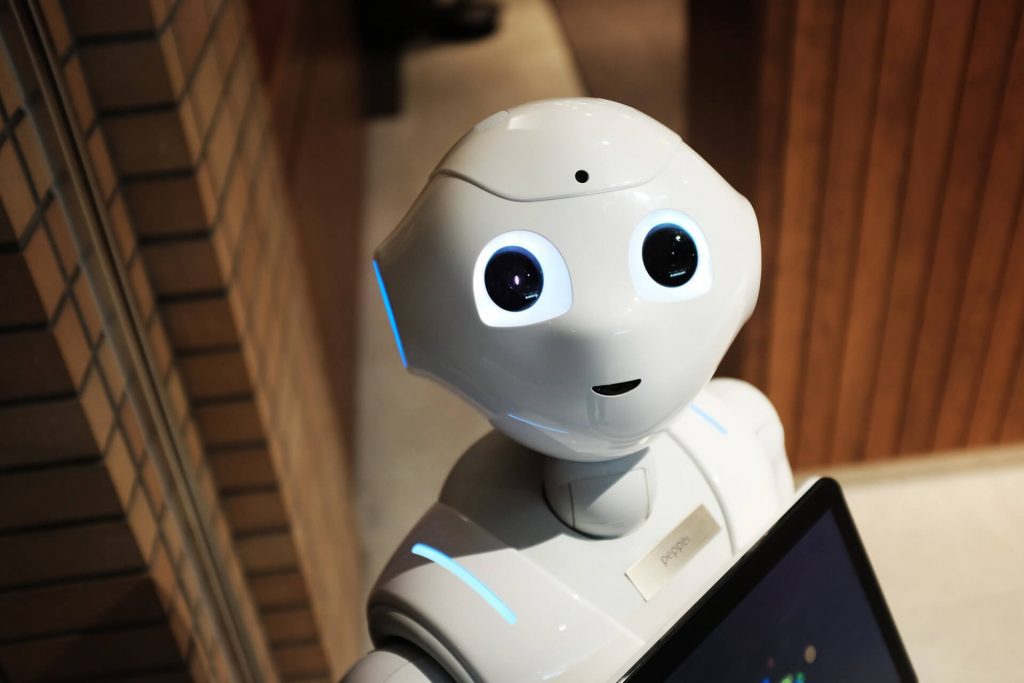
What’s the ROI on digital investments?
Increasing efficiency is key for investing in digital factories. Manufacturers overall expect solid gains from their companies’ efforts to digitize production. Over the next five years, they expect these initiatives to drive efficiency and revenue increases of 12% on average respectively.
PWC’s study found that the manufacturers who are planning to expand their digital factories intend to invest on average 6% of their total annual revenues over the next five years. Nearly half of them expect to see an ROI over five years, compared with just 3% who expect an ROI within one year. Digital training is one of those efforts that have a shorter ROI. Most of the companies are already in the process of going paperless with digital work instruction software like REWO.
Digitalization takes time, but companies can’t afford to miss it
Leading manufacturing companies are deploying a number of key technologies to digitize production as well as their entire supply chain. These include big data analytics solutions, end-to-end, real-time planning and connectivity, autonomous systems, digital twinning, and worker augmentation, among many others. These technologies provide significant efficiency gains and allow companies to produce highly customized products, often at a lot size one. But the full effect of digitization is only realized when companies are connected in real-time to their key suppliers and critical customers.