Every employee has a slightly different way of doing things. Each has a different background, different experience, different depth of skill, and a slightly different work process—and that introduces variation into a company’s workflow. The larger your operation, the more variation works its way into the production line. Work instructions are key to reducing variation, allowing manufacturers to improve quality and meet demand. Even better, written assembly line work instructions are a great training tool for new employees.
Are your work instructions worthless?
Let’s first touch on what good work instructions are not. Check the bottom list to see if any of these items apply to you:
- They are often way above the head of the operator, who would have a hard time referring to them if needed.
- Work instructions are prepared for ISO 9001 auditors and for customers, with the assumption that they don’t look carefully into the effectiveness of those instructions.
- There are often no image/photo. With text only, it takes more work to check and ensure that they correspond to the product being made. As a result, instructions are not engaging and operators don’t read them.
- The group leaders and supervisors know the instructions are meaningless, so they don’t use them as a standard. Ideally they would look periodically to see if an operator respects the applicable standard.
- Important quality considerations are not followed – for example checking 1 in 10 pieces for dimensional conformity.
- Important safety considerations are not followed – for example putting one’s hands in certain places to ensure they are never caught in a stamping machine.
- Important maintenance considerations are not followed – for example opening a compartment and cleaning the equipment.
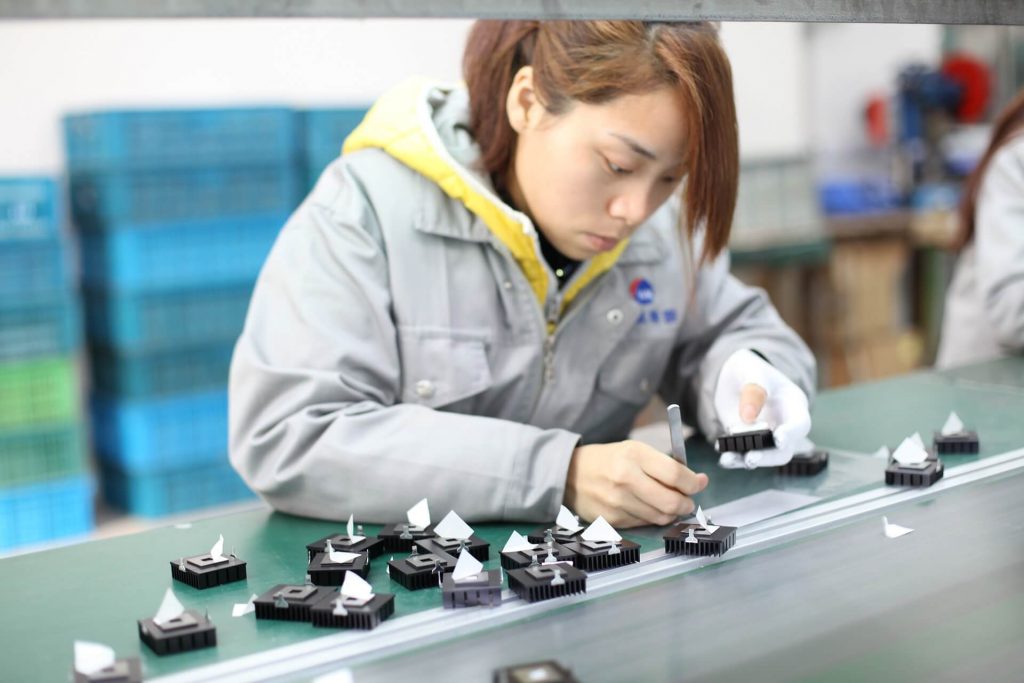
How to create great work instructions for your assembly line?
If your New Product Introduction (NPI) engineers haven’t prepared a standard work instruction sheet already, you’ll need to start writing them up. When writing your assembly line procedures, you should follow the bottom principles to ensure that your instructions are easy to follow.
Standardize the work on assembly lines (and elsewhere)
The core idea behind assembly line instructions is to follow ‘one best way currently known in this organisation’ so that if 5 people work on a particular job, they do it in the same way. If every operator has their own processes, it can make improving the way they work quite difficult. By following the standard manufacturing processes, one improvement to the work instructions can be applied immediately across the board and increase productivity, quality, and safety.
Write it with people who do the work on the assembly line every day
The people involved in the assembly line process day in and day out often know how to do a better job than most engineers sitting in your office. They might not try to do a good job in certain instances, for example, when they are paid by the piece and never have to do rework on the mess they have made. But, usually, they know how to do it.
Why not pull them out of production for an hour and work together to determine the optimal assembly line process? It not only gives you a better insight into the procedures, but it also trains them to think in a better way. And who knows, maybe they’ll keep thinking of it at the back of their mind, and in a week, they may think of a better process. You should even involve the production line or group leaders to push them to think outside the box. And, over time, they’ll learn how to solve problems too.
Get employee buy-in
Some factories treat their low-level employees as disposable resources. They tell them what to do, provide them with no training, and hope to replace them as fast as possible with automation. Don’t fall into that trap! Getting your employee’s feedback during the decision-making process can be a determining factor of your company’s success. Involving the workers when writing work instructions leads to sustainable improvement as you are getting their buy-in. Even if they disagree with an aspect of it, you’ll give them the opportunity to share their opinion and discuss it with their teams. And in the end, they might still be unhappy, but it is better to have received their input, and it may lead to less resistance from them.
Visualise standard work instructions
Once work instructions are written up, they need to be enforced. A leader or supervisor needs to be able to walk around and identify at a quick glance if the standards are being followed. Drawings can reflect the assembly line instructions much better than text paragraphs. We have seen many work instruction sheets written on bland templates with no graphic element to visualise the manufacturing process, and unsurprisingly, nobody reads them.
Include other elements in assembly line WI
When people think of standard work instructions, they think of a work sequence – first do this, next do that, etc. Having this is quite useful, especially if it also includes material movement and transformation as well as inspection and testing activities. But that’s not the only thing your manufacturing work instructions should encompass. Try to include a standard timing, i.e. how long is a particular process supposed to take to keep the line balanced. This shouldn’t be used to penalize workers or single out those who are too slow. Rather, it should put some healthy pressure and indicate who needs specialized training.
Train your process engineers
Do you want to develop your junior engineers? You can get them to work on projects to increase productivity based on the work instructions and other data they gather. Developing a combination table is useful when you want to go deep into the details. It shows the details of manual cycle time, automatic cycle time, walking time, and waiting time for 1 operator.