A standard operating procedure (SOP) is a set of step-by-step instructions compiled by an organization to help workers carry out routine operations. SOPs aim to achieve efficiency, quality output, and uniformity of performance while reducing miscommunication and failure to comply with industry regulations. But who will be the one to write standard operating procedures?
Who writes SOPs?
Ideally, Standard Operating Procedures should be written by a team that includes personnel from different areas. However, in the real world, they are often written by just one person. If this is the case, the person in charge of creating them should interview someone that performs the job, a supervisor, and the people in charge of ensuring that quality, health, safety, and environmental requirements are met. They should also have people from different areas review and comment before releasing the final Standard Operating Procedure.
Standard Operating Procedures should be clear and concise. Sentences must be as short as possible. People usually don’t want to read Standard Operating Procedures, they must, so making them clear and easy to read is essential.
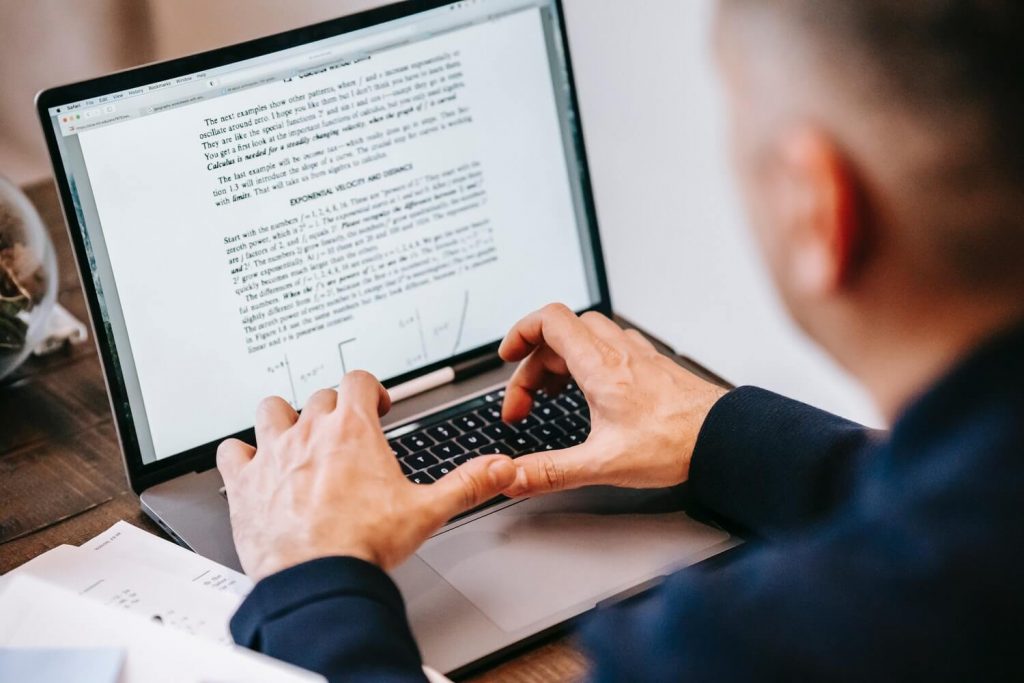
In manufacturing, it’s usually the process engineers that deal with SOPs
As a process engineer in a manufacturing company, you will be responsible for developing and implementing process strategies, managing process resources, optimizing current processes, and maintaining process documents. Ultimately, your job is to maintain the efficiency of production in order to reduce costs.
To ensure success as a process engineer you should have extensive experience in process design, excellent technical skills, and high-level analytical skills. A top-class process engineer can analyze a process system and implement simple yet effective changes to boost production. One of your main responsibilities would be to provide the Product Manager with process documents and standard operating procedures.
Why are standard operating procedures important?
Standard operating procedures provide benefits to any organization that incorporates them and ensures that they are kept up to date. The initial preparation of SOPs could be time-consuming, but the long-term return on investment (ROI) is well worth the effort. The high-level benefits of SOPs include the following: minimizing learning downtime, ensuring understanding of the role, ensuring consistency in the performance of duties.