Lean manufacturing addresses one of the worst things that can happen to any enterprise: waste. To not take full advantage of all of your resources is to lose efficiencies and, in so doing, stunt production. These neglected resources include everything from manufacturing project management tools, to the skills of the staff members. The core idea of lean manufacturing is actually quite simple; relentlessly work on eliminating waste from the manufacturing process. Lean manufacturing is also known as lean production, just-in-time manufacturing and just-in-time production, or just as JIT.
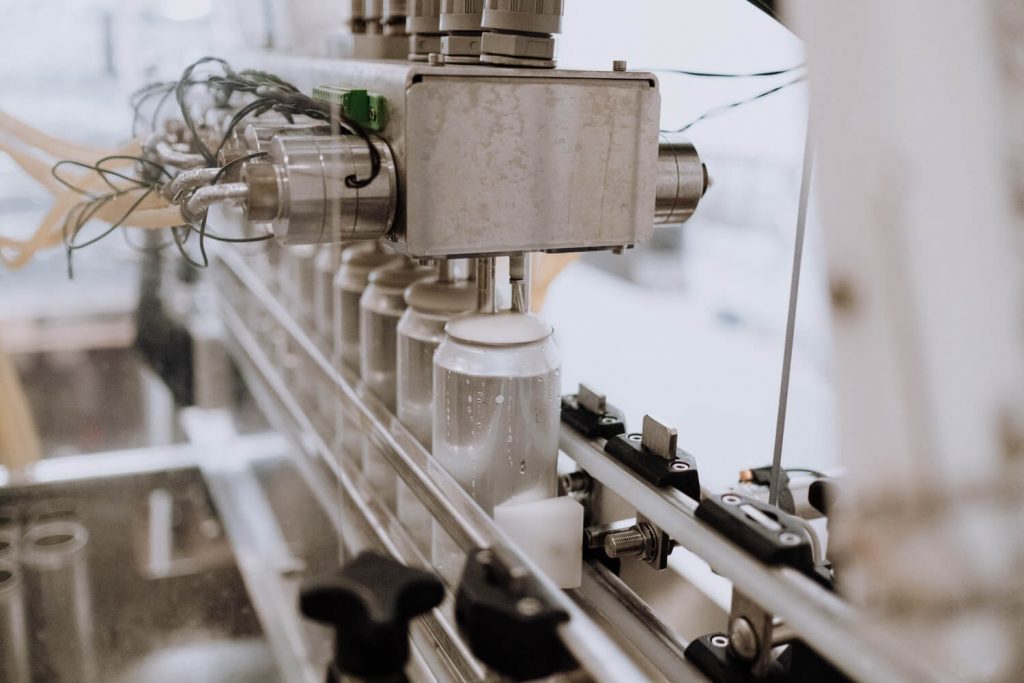
Who invented Lean Manufacturing?
Lean manufacturing is not a new concept–early versions of the method can be dated back to the beginning of the 20th century, when large-scale assembly line manufacturing was beginning to take root. As companies were beginning to think beyond local and regional distribution, as they were competing with both domestic and foreign competitors for market share, the need for efficiency, consistency, and speed gave birth to the scientific study of how things are produced.
Lean manufacturing we know today is derived from Toyota’s 1930 operating model “The Toyota Way”. The term “Lean” was coined in 1988 by John Krafcik, and defined in 1996 by James Womack and Daniel Jones to consist of five key principles: “Precisely specify value by specific product, identify the value stream for each product, make value flow without interruptions, let customer pull value from the producer, and pursue perfection.”
The exact reasons for adoption of JIT in Japan are unclear, but it has been suggested it started with a requirement to solve the lack of standardization. Researchers offers four reasons, paraphrased here. During Japan’s post–World War II rebuilding of industry:
- Japan’s lack of cash made it difficult for industry to finance the big-batch, large inventory production methods common elsewhere
- Japan lacked space to build big factories loaded with inventory.
- The Japanese islands lack natural resources with which to build products.
- Japan had high unemployment, which meant that labor efficiency methods were not an obvious pathway to industrial success.
Thus, the Japanese “leaned out” their processes. “They built smaller factories in which the only materials housed in the factory were those on which work was currently being done. In this way, inventory levels were kept low, investment in in-process inventories was at a minimum, and the investment in purchased natural resources was quickly turned around so that additional materials were purchased.
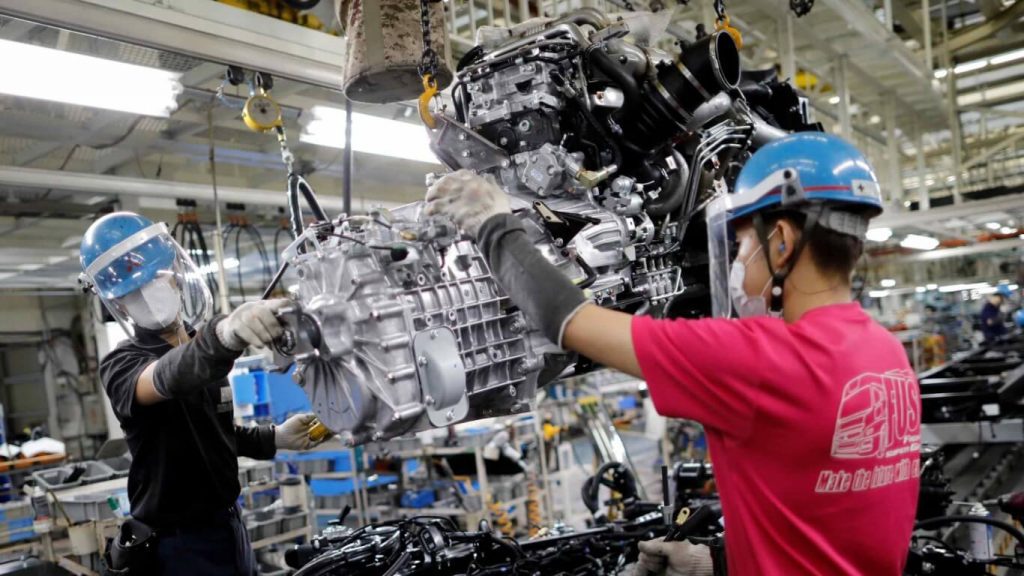
The importance or reducing waste
Waste is defined as any activity that does not add value from the customer’s perspective. According to research conducted by the Lean Enterprise Research Centre (LERC), fully 60% of production activities in a typical manufacturing operation are waste – they add no value at all for the customer.
Reducing or eliminating waste is essential to lean management, but the benefits of lean manufacturing can be different depending on who is asked. Some say it is increasing company profit while others maintain its improvements are solely to create customer value and increase customer satisfaction. What is for sure is having well defined and efficient processes will bring countless benefits to all sections of your organization.