Die verarbeitende Industrie befindet sich in einem seismischen Wandel. Da erfahrene Arbeitskräfte in den Ruhestand gehen und eine jüngere, technikaffine Generation in die Belegschaft eintritt, wird die Lücke in Bezug auf Fähigkeiten und Erfahrung immer deutlicher. Unternehmen müssen nicht nur Wege finden, diese Lücke zu schließen, sondern auch ihre Schulungs- und Arbeitsmethoden anpassen, um den Erwartungen der neuen Arbeitskräfte gerecht zu werden. Eine der effektivsten Strategien ist die Umstellung von traditionellen papierbasierten Arbeitsanweisungen auf digitale Lösungen.
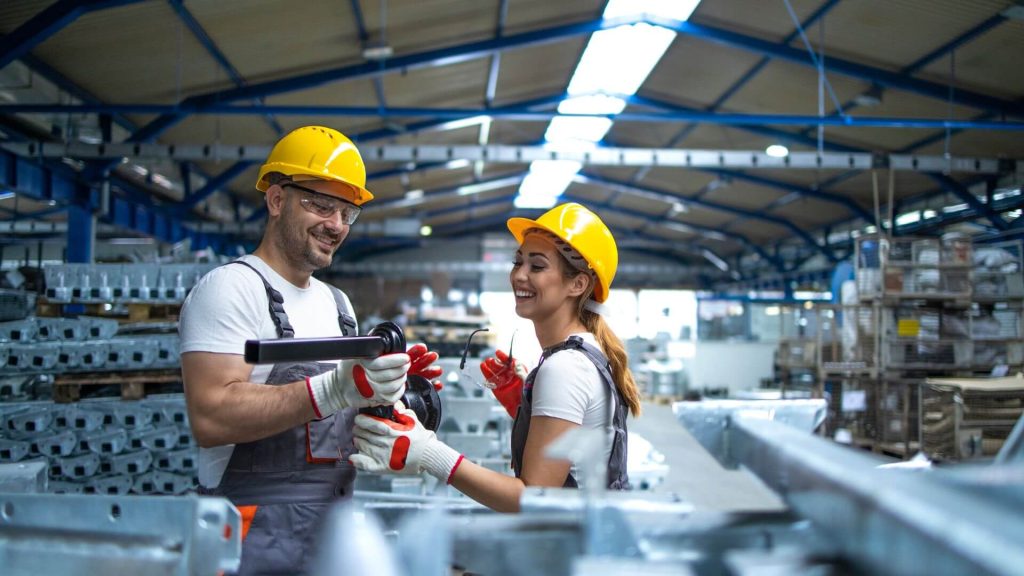
Die wachsende Qualifikationslücke in der Fertigung
Die Qualifikationslücke im verarbeitenden Gewerbe ist kein Geheimnis. Laut einer Deloitte-StudieBis 2030 könnten allein in der verarbeitenden Industrie der USA mehr als 2,1 Millionen qualifizierte Arbeitskräfte fehlen. Diese Lücke bedroht die Produktivität, die Innovation und das gesamte Wachstum der Branche.
Mehrere Faktoren tragen zu dieser Qualifikationslücke bei:
- Ausscheidende Arbeitskräfte: Die geburtenstarken Jahrgänge, die einen bedeutenden Teil der Arbeitskräfte im verarbeitenden Gewerbe ausmachen, gehen in raschem Tempo in den Ruhestand.
- Mangel an neuen Talenten: Jüngere Generationen übersehen oft die Fertigung als Berufswahl, weil sie ein veraltetes Bild von der Branche haben.
- Die Komplexität der modernen Fertigung: Fortschritte in der Automatisierung, Robotik und Datenanalyse erfordern eine Reihe neuer Fähigkeiten, die viele der derzeitigen Arbeitnehmer nicht besitzen.
Die Erwartungen der jüngeren Arbeitnehmer
Millennials und Gen Z bringen neue Perspektiven und hohe Erwartungen an den Arbeitsplatz mit. Im Gegensatz zu ihren Vorgängern sind diese Digital Natives mit der Technologie als integralem Bestandteil ihres Lebens aufgewachsen. Ihre Lernpräferenzen spiegeln dies wider:
- Visuelles Lernen: Jüngere Arbeitnehmer bevorzugen Video-Tutorials, interaktive Anleitungen und visuelle Hilfsmittel gegenüber langen, textbasierten Handbüchern.
- Sofortiger Zugang: Sie erwarten, dass Informationen auf Smartphones, Tablets oder anderen digitalen Geräten leicht zugänglich sind.
- Kontinuierliches Feedback: Sie schätzen sofortiges Feedback und Möglichkeiten zum kontinuierlichen Lernen.
Herkömmliche Schulungsmethoden und papierbasierte Arbeitsanweisungen werden diesen Erwartungen nicht gerecht, was zu mangelndem Engagement, Fehlern und geringerer Produktivität führt.
Warum digitale Arbeitsanweisungen die Lösung sind
Digitale Arbeitsanweisungen sind eine Antwort auf die Herausforderungen des Fachkräftemangels und passen sich gleichzeitig den Bedürfnissen jüngerer Arbeitnehmer an. Hier sind die wichtigsten Vorteile:
1. Verbessertes Engagement
Interaktive und multimediale Anleitungen machen das Lernen interessanter. Videos, Animationen und Augmented Reality (AR)-Tools können komplexe Prozesse effektiver veranschaulichen als Text oder statische Bilder.
2. Verbesserte Zugänglichkeit
Digitale Plattformen ermöglichen es den Mitarbeitern, jederzeit und überall auf Anweisungen zuzugreifen. Ob in der Werkstatt oder bei Schulungen außerhalb des Unternehmens, die Mitarbeiter können ihre Geräte nutzen, um die benötigten Informationen zu finden.
3. Schnelleres Onboarding
Dank intuitiver, schrittweiser Videoanleitungen können neue Mitarbeiter ihre Aufgaben schnell verstehen, ohne auf umfangreiche persönliche Schulungen angewiesen zu sein. Dies reduziert Ausfallzeiten und beschleunigt die Produktivität.
4. Updates in Echtzeit
Fertigungsprozesse entwickeln sich weiter, und das sollten auch die Anweisungen. Digitale Arbeitsanweisungen können in Echtzeit aktualisiert werden, so dass die Mitarbeiter immer über die aktuellsten Informationen verfügen.
5. Fehlerreduzierung
Klare, visuelle und interaktive Anweisungen minimieren das Risiko von Fehlern und erhöhen die Produktqualität und die Sicherheit der Mitarbeiter.
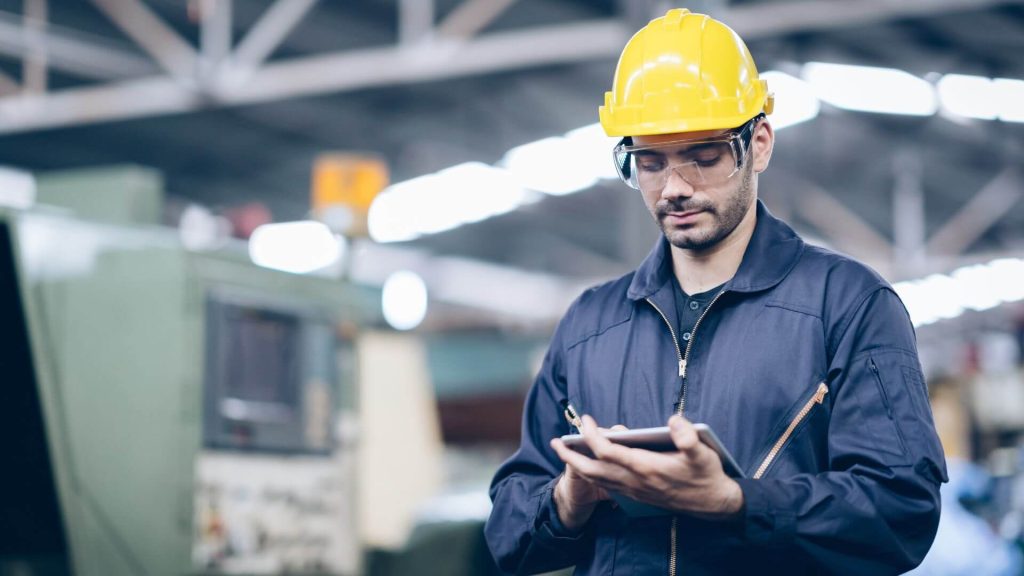
Digitale Arbeitsanweisungen implementieren
Die Umstellung auf digitale Arbeitsanweisungen muss nicht überwältigend sein. Hier sind einige Schritte für den Anfang:
Schritt 1: Bewerten Sie Ihre aktuellen Prozesse
Bewerten Sie Ihre bestehenden Arbeitsanweisungen. Identifizieren Sie Prozesse, die häufig zu Fehlern oder Verwirrung führen, und priorisieren Sie diese für die Digitalisierung.
Schritt 2: Wählen Sie die richtigen Tools
Wählen Sie eine Plattform, die Ihren Bedürfnissen entspricht. Tools wie REWO bieten intuitive Schnittstellen für die Erstellung und Verwaltung videobasierter Arbeitsanweisungen. Funktionen wie mehrsprachige Unterstützung und AR-Integration können ihre Effektivität weiter erhöhen.
Schritt 3: Beziehen Sie Ihr Team ein
Beziehen Sie Ihre Mitarbeiter in den Übergangsprozess ein. Holen Sie Feedback zu den bevorzugten Lernmethoden ein und testen Sie die digitalen Arbeitsanweisungen mit einer kleinen Gruppe, bevor Sie sie in größerem Umfang einsetzen.
Schritt 4: Schulung und Unterstützung
Bieten Sie Schulungen an, um sicherzustellen, dass die Mitarbeiter mit dem neuen System vertraut sind. Bieten Sie fortlaufende Unterstützung und fördern Sie Feedback, um die digitalen Anweisungen kontinuierlich zu verbessern.
Schritt 5: Messen und Optimieren
Überwachen Sie die Auswirkungen digitaler Arbeitsanweisungen auf Produktivität, Fehlerquote und Mitarbeiterzufriedenheit. Nutzen Sie diese Daten, um Ihren Ansatz zu verfeinern und den ROI zu maximieren.
Blick in die Zukunft: Die Zukunft der Arbeitsanweisungen
Mit der Weiterentwicklung der Fertigung wird die Einführung digitaler Arbeitsanweisungen weiter zunehmen. Aufkommende Technologien wie künstliche Intelligenz (KI) und das Internet der Dinge (IoT) werden die Fähigkeiten dieser Systeme weiter verbessern. Zum Beispiel:
- KI-gestützte Anpassung: KI kann die Leistung von Mitarbeitern analysieren und personalisierte Empfehlungen zur Verbesserung der Effizienz geben.
- IoT-Integration: IoT-fähige Geräte können Echtzeit-Feedback liefern und Anweisungen automatisch auf der Grundlage der Maschinenleistung aktualisieren.
Fazit
Die verarbeitende Industrie steht an einem Scheideweg. Um den Fachkräftemangel zu beheben und die nächste Generation von Arbeitnehmern zu beschäftigen, sind innovative Lösungen erforderlich. Digitale Arbeitsanweisungen sind nicht nur ein "Nice-to-have", sondern eine Notwendigkeit, um in der heutigen schnelllebigen Umgebung wettbewerbsfähig zu bleiben.
Durch den Einsatz von Tools wie REWO und einen modernen Ansatz für Schulung und Betrieb können Hersteller die Kluft zwischen den Generationen überbrücken, Fehler reduzieren und langfristigen Erfolg sicherstellen. Die Zeit zum Handeln ist jetzt gekommen. Investieren Sie in digitale Arbeitsanweisungen und machen Sie Ihre Belegschaft fit für die Zukunft.
Sie möchten Ihre Produktionsabläufe modernisieren? Erfahren Sie mehr über REWO und wie Sie damit Ihre Trainings- und Arbeitsanweisungen noch heute verändern können!